ansys workbench tutorial ppt
Opening the ANSYS Workbench Environment From the program menu list open the ANSYS 150 folder and select Workbench 150. Is certified to ISO 90012008.
Chapter 1 Ansys Workbench Ppt Download
This tutorial introduces you to the ANSYS workbench and Fluent environments.
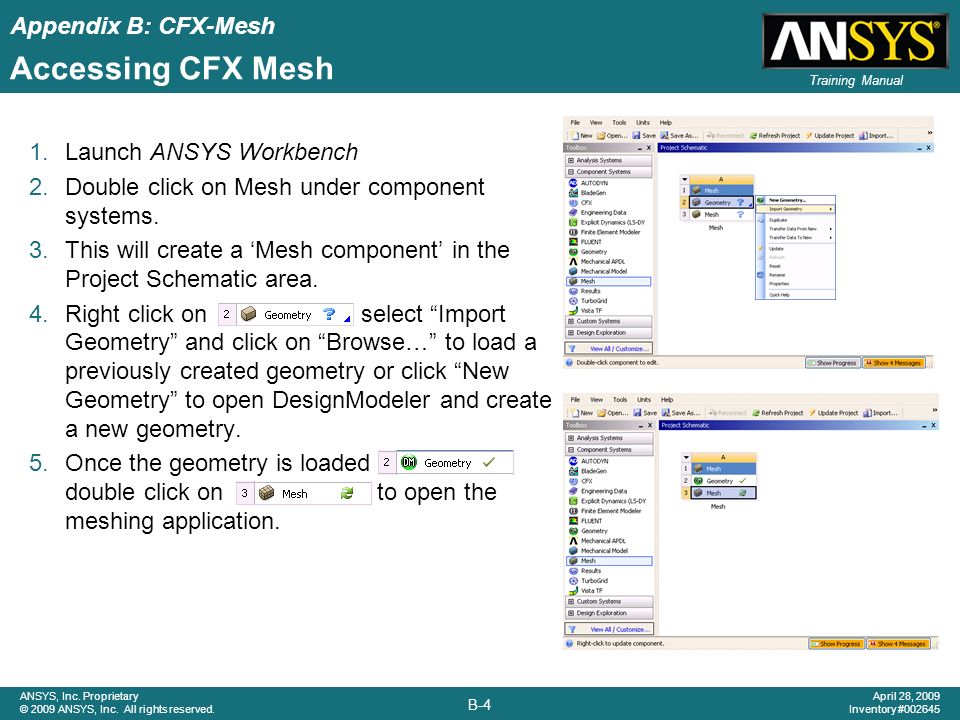
. Define material properties and real constants. Let the X-Y plane be the plane of analysis. Become an expert in FEA by applying these 41 step-by-step PDF tutorials in ANSYS Workbench.
Once ANSYS is active and you have closed the popup window presented you will be able to view the Project tab. A summary of ANSYS Strengths Finite Element Analysis FEA is a way to simulate loading conditions on a design and determine the designs response to those conditions. Surner SRES Sanjivani college of engineering Kopargaon 2.
Ad Learn ANSYS online at your own pace. Define element types to be used. Depending on where you are attempting to access ANSYS it may be under ANSYS 130 ANSYS or Class.
The nonzero stresses - σ x σ y and τ xy lie in the - YX plane and do not vary in the Z direction. Create structural frame defined in Assignment 01. The final mesh is shown below along with labels for the edges.
Once ANSYS opens your computer monitor should look comparable to. ANSYSRevit ArchitecturePCB Designing Training CentreOrcad Capture Pspice Courses in Anna Nagar 1 - If you are looking for the certified ANSYS software teaching centre in Anna Nagar then CADD Centre will be your right choice. Ansys workbench tutorial ppt.
Defining points manually 2. Further the other stresses σ zτ yz and τ zx are all zero for this kind of geometry and loading. ANSYS Workbench with a New Fluent-Based Fluid Flow Analysis System 3.
There are some differences in ANSYS APDL and. ANSYS Workbench is comprised of various applications some examples. 4 Postprocessing view results View displacements.
This view should look like the view below. Workbench Doc 01 1. These panels include ANSI Homeland Defense and Security Standardization Collaborative ANSI Nanotechnology Standards Panel ID Theft Protection and ID Management Standards and ANSI Energy Efficient Standardization Coordination Collaborative.
ANSYS Fluent Tutorial Part 1. This tutorial assumes that ANSYS Workbench is running but no projects are open. Import geometry Cylinder_Surfaceigs to design modeler 2.
It is easy to see at-a-glace how a model has been built and determine which files were used for a particular simulation pairing geometry files to solver runs. 5 x 10 x 01 cm. No APDL tutorials exist on this website TUTORIAL 41.
Start today and improve your skills. Identify domain What results are you looking for ie. 2 FATIGUE CRACKS PROPAGATING IN STEEL.
Example of a simple plate or bar with a hole. ANSYS FLUENT Tutorial Guide ANSYS Inc. MAE 656 cba Dr.
Introduction to Workbench in ANSYS 12 - Fernando Ba 2011-08-12 Introduction to Workbench in ANSYS Introduction to ANSYS ICEM CFD - oss. ANSYS WORKBENCH STATIC STRUCTURAL FEA OF 1 VS. Introduction to the CFD Methodology 1.
Start ANSYS Workbench and follow the sequenced steps using the abbreviations shown below. Apply loads and boundary conditions. ANSYS has enhanced capabilities in meshing contacts physics interaction solver performance and ease of use HPC technology is needed for getting the results faster.
ANSYS Workbench Tutorial - Introduction to Static Structural. Introduction Welcome to the ANSYS Workbench introductory training course. Introduction to ANSYS Workbench 1.
If it is not. Using point data Frame Nodestxt In this second case the roof beams have a cross section. Check out this guide to understanding ANSI safety standardsWhere to Find.
Enter elbow for the name of the analysis system. Upon completing this tutorial you will understand. It may take some time for ANSYS to open.
2-2 ANSYS Tutorial A state of Plane Stress exists in a thin object loaded in the plane of its largest dimensions. Proprietary 2009 ANSYS Inc. Basic tutorial on how to use ANSYS workbench.
Xavier Martinez 2012 02. Click for video with results on. This training course covers the basics of using Simulation in performing structural and thermal analyses.
1 Drag Mesh component to project schematic 3 Toggle Analysis Type to 2D 2 Select Geometry 4 Launch DM Double clickright click Geometry 15. Open ANSYS Workbench Click on the Start button then click on All Programs. To ANSYS ICEM CFD Lecture 1 Introduction to ANSYS ICEM CFD 2 2011 ANSYS Inc.
Define Your Modeling Goals Customer Training Material What results are you looking for i e pressure drop mass flow rate Problem Identification 1. 01042013 Hexa Meshing Introduction to ANSYS ICEM CFD Introduction to ANSYS ICEM CFDdl. Mechanical for performing structural and thermal analyses using the ANSYS solver Meshing is also included within the Mechanical application Mechanical APDL for performing advanced mechanical and multiphysics analyses using the traditional ANSYS user interface.
2 Preprocessing make model Specify title. March 22 2015 Release 140. This tutorial provides instructions for creating a simple two-dimensional mesh that is used to simulate the boundary layer on a flat plate.
Once you locate ANSYS click on the the workbench button. Double-click the Fluid Flow Fluent label underneath the analysis system if it is not already highlighted. May 5 2 09 I nve tory 02593 Workbench - Mechanical Introduction 120 Chapter 5.
Inlet Plate Outlet Symmetry Top Set Workbench options for a new FLUENT project 1. This ANSYS Workbench training centre in Anna Nagar serves all your need of professional training and gets more career opportunity in the IT sector. Workbench is used to launch the individual software components and used to transfer data between them.
ANSYS workbench environment o Create a new project create geometry mesh the domain identify and name boundary conditions grid adaptation Flow simulation in Fluent o Export mesh to Fluent apply boundary. Release 140 Southpointe November 2011 275 Technology Drive Canonsburg PA 15317 ANSYS Inc. DC Double Click with Left Mouse Button SC Single Click with Left Mouse Button RMB Right Mouse Button Selection DD Drag and Drop Hold Left Mouse Button down on item while dragging it to new location and then release it ie Copy or Move 1.
Join millions of learners from around the world already learning on Udemy. ANSYS Workbench is a convenient way of managing your simulation projects. Select the Save option under the File menu in ANSYS Workbench.